Banpu has been going through its transformation to create sustainable growth as an International Versatile Energy Provider offering the best-in-class energy solutions with our extensive expertise in integrated energy in 10 countries across Asia-Pacific. One of the keys to success of Banpu Transformation is driving the organization through the Digital Transformation process, which we have continuously been implementing for the last 3 years, to create modern digital technology for business and deliver future energy for sustainability with full efficiency to our stakeholders with our standpoint on “Smarter Energy for Sustainability”.
The Company has established Digital Center of Excellence (DCOE) in 2018 to drive Banpu through digital transformation. It leverages smart innovation, technologies and digital concept and applies new way of working; “agile working”, across the organization to promote work efficiency in every department, and to develop products and services to better meet needs of all customer segments; businesses (B2B), consumers (B2C) and the Government (B2G).
Currently, digital transformation has been rolled out in four countries: Thailand, Indonesia, Australia, and China. DCOE in Thailand is a centralized team for developing strategy and working plan including creating and sharing smart ways of working among DCOEs in those countries to establish implementation standards and drive Banpu transformation with maximum efficiency.
Digital product showcase in Thailand
DCOE Thailand is a hub for supporting Banpu’s businesses in 10 countries. Technology has been implemented to boost productivity of employees, equipment, and machines to be more accurate, faster, and less errors. DCOE Thailand has a full team of digital experts, including Digital Coach, Scrum Master, User Experience Team and Developer. Therefore, it has covered the development of digital products in two parts:
1. Link-ups with every business unit at the head office in Thailand
Develop digital products to remedy pain points as they arise, and improve work processes and efficiency of departments in the Company. Currently, there are over 20 cases of digital products in the pipeline.
2. Supporting DCOEs in China, Indonesia, and Australia
Develop digital products as requested. DCOE Thailand has dedicated digital experts to share their knowledge and experience, and take roles in the development team to deliver a completed job with smooth and efficient operations.
The product development process applies Design Thinking to solve problems and genuinely meet users’ needs. It also implements Agile workstyles which require continuous testing of product concepts for maximally cost-effective outcomes in terms of finance, time, and human resources.
Highlighted Digital Products from Thailand
1. Artery
An application for management of large volumes of customers’ insight data on online systems by storing customer profiles in databases and categorizing groups of customers based on points. The points are automatically calculated by the assessment of financial status, credibility, and customer’s risk management. The results are used by related departments when granting credit to customers. The credit-approval system on application is easy-to- use to monitor status at every stage of the process. There is also an Analytic Dashboard providing an overview.
• Locations: Marketing, Sales and Logistics (MS&L) in Thailand, Japan, Australia, Indonesia and China
• Benefits:
– Reduce human error and redundant work by using systematic customer database
– Reduce about 20% of time spent on a credit approval work process as the application can be used easily online for instant status verification
– Better decision making with adequate key data
– Reduce bad debts and overdue amounts by approving appropriate credit amounts for each customer
2. Hauling Road Designer
An application for designing efficiency coal hauling process with easy-to-use and flexible digital systems. The application can store relevant data such as truck size, attributes of hauling load, mine parameters, and the width and state of roads. As well, it displays data to give an overall picture, which can be used to efficiently design coal hauling plans and estimate costs more accurately.
• Locations: Trubaindo and Bharinto Mines, Indonesia
• Benefits:
– More accurately estimated coal hauling costs given adequate data
– Plan coal hauling in advance to prepare adequate necessary resources
– Improve productivity of the coal hauling process
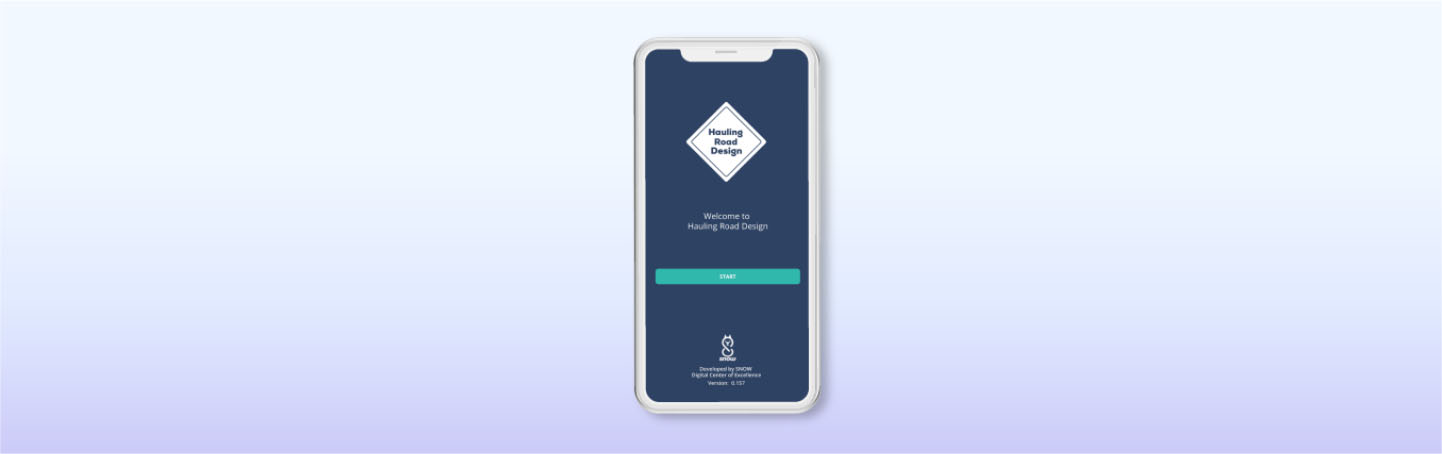
Digital Product Showcase in Indonesia
In 2018, DCOE Indonesia has been implementing modern technology to boost the productivity of mining operations in terms of both production and logistics, while also upskilling employees to achieve the end goal of a Digital Mine. It makes coal production become more flexible and align with coal demand and price, even the weather, which are key factors impacting production efficiency. There is also a consideration of reducing environmental and social impacts. As a result, digital products have been developed in a total of 47 cases, such as:
1. Mine Operation Collaboration Application (MOCA)
A digital solution which improves an efficiency of mine pit issues reporting by operations team leading to solutions to solve problems of relevant departments and executives. We changed the way of working from radio communication which was less responsive to operational needs and unable to review the past records that can be used to make decisions about the same problems in the future. Therefore, MOCA is used to report detected data or problems in real time. MOCA collects redundant and scattered data and put them into a system, and makes it easier to trace back the past records. It also provides more quickly and efficiently collaboration among all stakeholders who are involved in the decision-making process.
• Locations: Trubaindo, Indominco and Bharinto mines
• Benefits:
– Faster process of reporting and compiling key production data
– Related departments can make quick decisions to remedy unexpected issues.
– More efficient collaboration between internal and external stakeholders
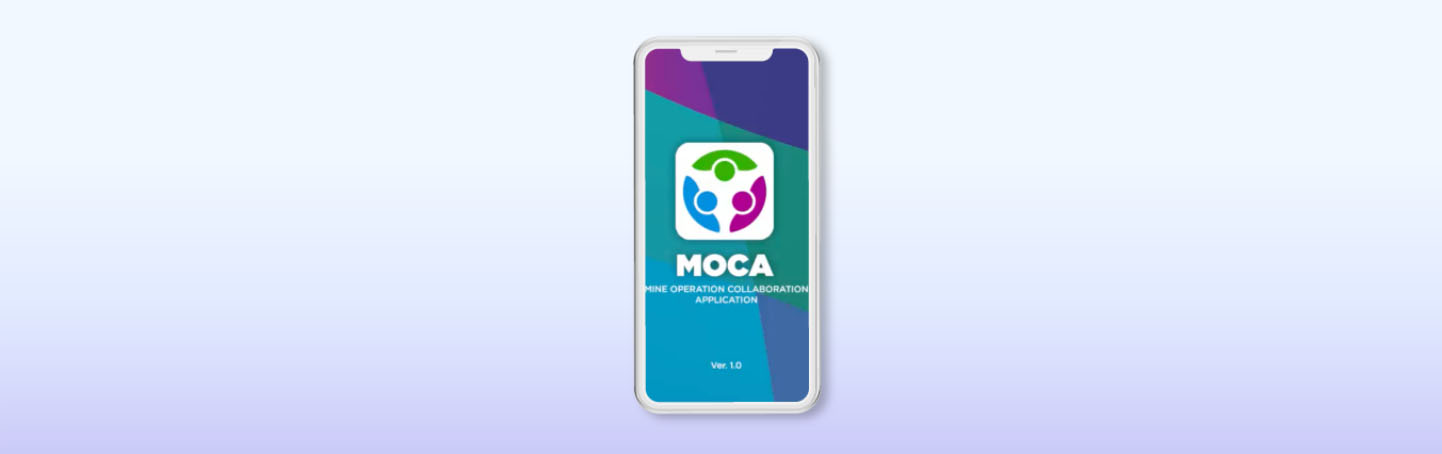
2. Monitoring Enhancement Reliability of Coal Quality (MERCY)
A digital solution which provides transparency of coal production activity from pit to port, enabling the planning of coal production and logistic systems to meet customer demand more efficiently, both qualitatively, quantitatively and in delivery timeframes. MERCY was developed as a single system with faster data visibility for all lab processes with automated analysis and distribution. For instance, coal production volumes can be tracked from the Smart Truck Scale system, part of MERCY. This replaces the method of counting trucks to calculate capacity with the method of weighing to provide the actual production volume.
• Locations: Trubaindo, Indominco and Bharinto mines
• Benefits:
– Planning and changing coal production plans to match with customer demand with better efficiency within agreed time
– Reduce data collection errors from human error with an integrated and automatic system
– Reduce required human and time resources in compiling data and distributing report to related departments
Digital Product Showcase in Australia
Since 2018, DCOE Australia has been developing and deploying digital technology to improve operational efficiency of staff and machines to be more precise and faster, while reducing errors from both humans and equipment. It also boosts productivity by managing costs. As a result, there are 14 use cases, for instance:
1. Energy Management platform
A platform to monitor energy consumption in real time on a 4G network using IIoT (Industrial Internet of Things) integrations of all major equipment on the SwitchDin’s cloud analytic platform. This is a local startup based in Newcastle, New South Wales, whose platform has been validated with numerous utility, commercial and industrial clients around Australia. The platform can anticipate energy consumption in mine sites, and analyze demand in Australia’s energy markets to efficiently plan energy management at mine sites for optimal cost-effectiveness.
• Locations: All of Centennial’s mine sites
• Benefits:
– Reduced energy costs
– Improved efficiency of energy generation, including energy from the grid and net selling to the grid, such as the solar energy project in Airly.
– Sustainable operations by generating power for self-use, from the “Behind the meter” project that uses renewable energy.
Digital Product Showcase in China
In 2020, China DCOE has been implementing technology solutions in power business for more efficient operations of both people and machines. Also, they result in increased productivity and appropriate cost control. The China DCOE developed digital products in 4 categories: digital processing, advanced analysis, automation and robotics, and mixed levers in 12 use cases, for instance:
1. Solar Inventory Management System
Technology was applied to develop supply and storage process using an online system for procurement and supplier management to be easier and more convenient. The system features unified material code to record complete inventory items and prepare accurate valuation of inventory with visual warehouse design. This enables convenient unified management of multi-stations. These can standardize inventory management and enhance process efficiency.
• Locations: All solar power plants in China
• Benefits:
– Saved Human Resources costs of RMB 10,000/year (approx. THB 50,000)
– Saved time with improved and standardized inventory management.
– Reduced times of repeat purchases, leading to efficient control of inventory costs with accurate and timely inventory information
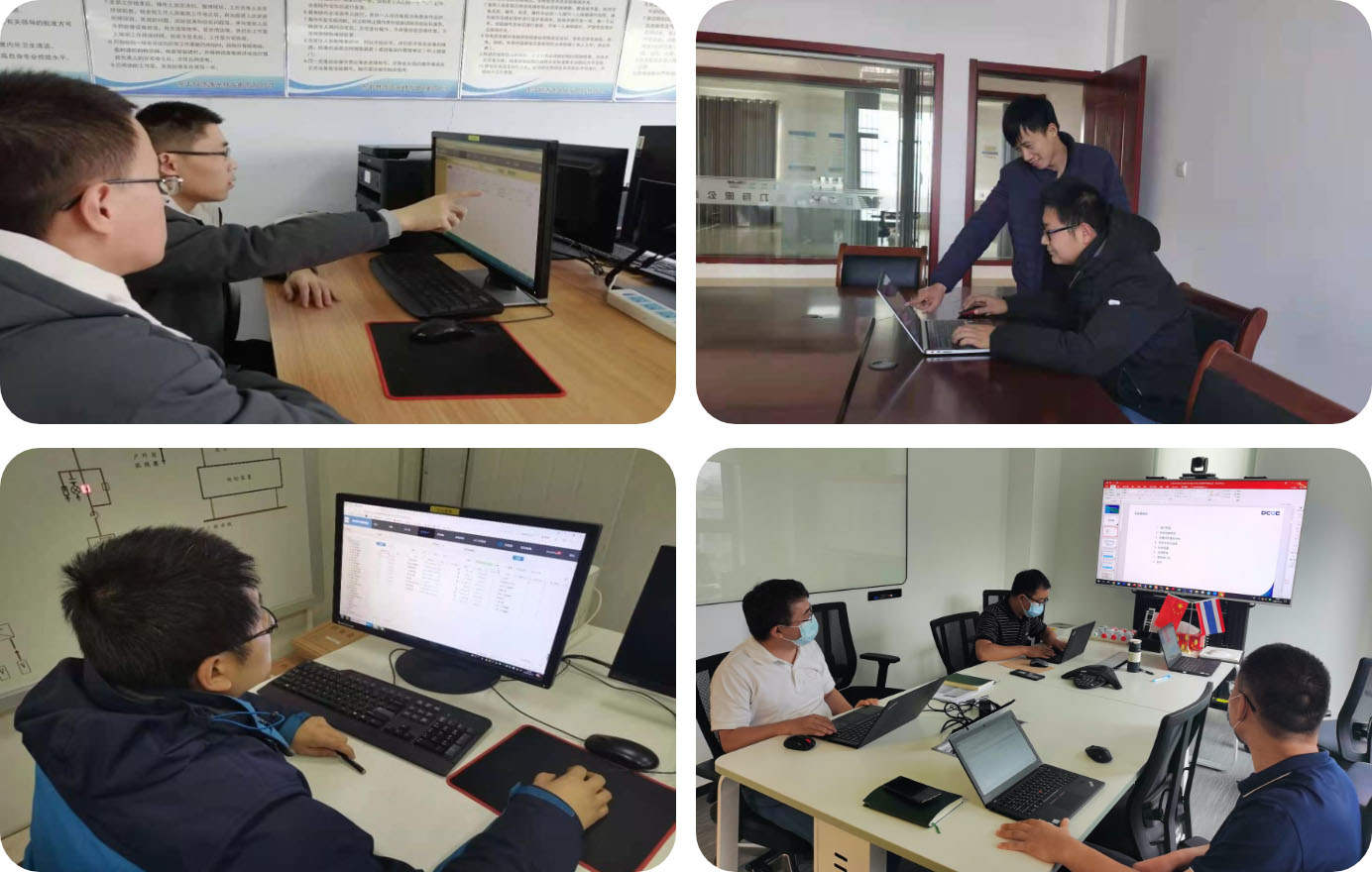
2. Digital Work Permit
Work Permit system for management of safety measures in a high-risk manner or area for operation and maintenance staff to prevent accidents and dangers. It is designed to be easy to use and to monitor approval process management of work permits in real time together with face and fingerprint recognition function which tightens the requirements of permission request. It also has the features of to-do list reminder and quickly reach of safety standard information. These can improve employee experience.
• Locations: Luannan power plant
• Benefits:
– Saved Human Resources costs of RMB 50,271/year (approx. THB 250,000)
– Reduced time taken in approval process by 30%
– Improved safety measures and implementation quality, from easier employee access to data and safety criteria
– Better employee experience with simple and convenient function
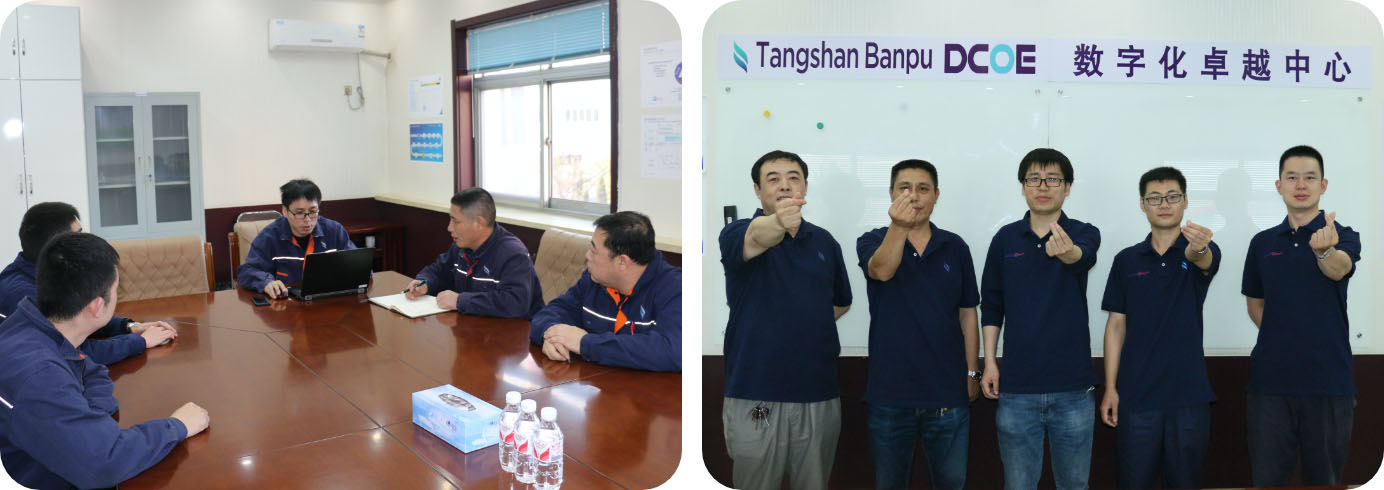